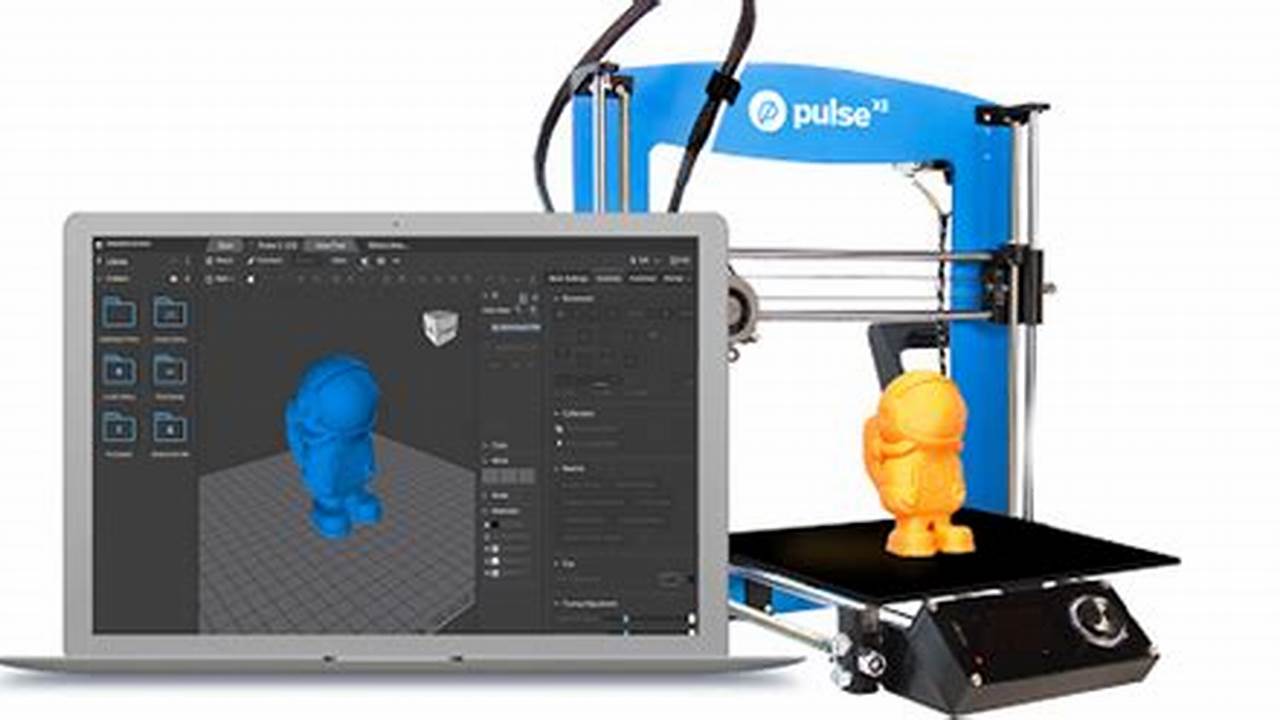
Product design software for 3D printing, or software dedicated to designing 3D models for additive manufacturing, holds the key to unlocking the full potential of this transformative technology. An apt example is the automotive industry, where product design software is used to create intricate prototypes and end-use parts quickly and cost-effectively.
Its relevance lies in the growing demand for personalized and customized products, the need for faster time-to-market, and the reduction of manufacturing costs. Its benefits include improved design accuracy, greater design freedom, and reduced lead times. A key historical development was the introduction of computer-aided design (CAD) software, which laid the foundation for modern product design software for 3D printing.
In this article, we delve into the capabilities, functionalities, and future prospects of product design software for 3D printing. We explore industry best practices, emerging trends, and the impact of this technology on various sectors.
Product Design Software for 3D Printing
Product design software for 3D printing is crucial for the digital creation of 3D models that can be physically realized through additive manufacturing. Key aspects of this software include:
- Modeling tools
- Simulation capabilities
- Material libraries
- Slicing engines
- Support generation
- Build optimization
- Integration with CAD
- Cloud collaboration
- User interface
- File formats
These aspects encompass the core functionalities of product design software for 3D printing, from creating and modifying 3D models to preparing them for printing. They enable designers and engineers to leverage the full potential of 3D printing technology, fostering innovation and accelerating product development.
Modeling tools
At the heart of product design software for 3D printing lie modeling tools, a comprehensive suite of capabilities that empowers designers and engineers to create and modify 3D models with precision and efficiency. These tools form the foundation for all subsequent , enabling the realization of complex geometries and functional prototypes.
-
Solid modeling
Solid modeling allows users to create precise 3D models with defined dimensions and material properties, enabling the accurate representation of physical objects. -
Surface modeling
Surface modeling focuses on creating smooth, curved surfaces, often used for organic shapes and aesthetic designs. -
Parametric modeling
Parametric modeling links design parameters to geometric features, allowing for quick and easy model updates when design changes are made. -
Boolean operations
Boolean operations combine or subtract solid models, enabling the creation of complex shapes by merging, intersecting, or cutting different forms.
The versatility and power of modeling tools in product design software for 3D printing empower designers to push the boundaries of innovation, creating models that were once impossible to manufacture using traditional methods. They streamline the design process, reduce errors, and facilitate collaboration, ultimately accelerating product development and bringing innovative ideas to life.
Simulation capabilities
Simulation capabilities play a critical role within product design software for 3D printing, allowing designers and engineers to evaluate the performance and behavior of their designs virtually before committing to physical production. This enables them to identify and address potential issues early on, saving time, resources, and minimizing the risk of costly mistakes.
One key aspect of simulation capabilities is the ability to simulate real-world physical forces, such as stress, strain, and deformation, on 3D models. This helps designers optimize their designs for strength, durability, and functionality. For instance, a designer can simulate the stress distribution on a prototype part under various loading conditions, enabling them to identify weak points and reinforce them accordingly.
Simulation capabilities also extend to fluid dynamics, allowing designers to analyze fluid flow and heat transfer within their designs. This is particularly important for products involving liquids or gases, such as medical devices or fluid handling systems. By simulating fluid flow patterns, designers can optimize the efficiency and performance of their products, ensuring they meet the desired functional requirements.
In summary, simulation capabilities are a crucial component of product design software for 3D printing, enabling designers and engineers to validate and optimize their designs before physical production. By leveraging simulation tools, they can minimize the risk of costly errors, reduce development time, and create products that perform reliably and efficiently in the real world.
Material libraries
Material libraries are a critical component of product design software for 3D printing, providing a comprehensive database of materials with defined properties and characteristics. These libraries empower designers and engineers to select the most suitable materials for their designs, ensuring optimal performance and functionality of the final printed parts.
The integration of material libraries within product design software streamlines the design process and reduces the need for manual research and experimentation. Designers can browse through a wide range of materials, including plastics, metals, ceramics, and composites, each with unique properties such as strength, flexibility, temperature resistance, and biocompatibility. By selecting the appropriate material for their design, designers can ensure that the final printed part meets the specific requirements of the application.
For instance, in the medical industry, product design software with extensive material libraries enables the creation of 3D printed implants and prosthetics tailored to individual patients’ needs. By selecting biocompatible materials with the required strength and flexibility, designers can create patient-specific implants that offer a precise fit and optimal functionality. Similarly, in the aerospace industry, material libraries within product design software help engineers choose lightweight and durable materials for aircraft components, optimizing performance and fuel efficiency.
In summary, material libraries in product design software for 3D printing play a pivotal role in enabling designers and engineers to make informed decisions about material selection. This leads to optimized designs, improved product performance, and faster time-to-market, ultimately driving innovation and advancing various industries.
Slicing engines
Slicing engines are critical components within product design software for 3D printing, responsible for preparing 3D models into a format suitable for additive manufacturing. They play a central role in ensuring successful and efficient printing by generating instructions that guide the 3D printer’s movements and material deposition.
The process of slicing involves dividing the 3D model into thin layers, determining the optimal path for the printer’s nozzle, and generating support structures when necessary. Slicing engines consider factors such as layer thickness, infill density, and print orientation to optimize print time, material usage, and part quality. Advanced slicing engines also offer features such as adaptive slicing, which adjusts slicing parameters based on the model’s geometry, leading to improved print quality and reduced printing time.
Real-life examples of slicing engines integrated within product design software include Cura, PrusaSlicer, and Simplify3D. These engines provide user-friendly interfaces, comprehensive slicing parameters, and advanced features that cater to various 3D printing technologies and materials. They enable designers and engineers to fine-tune their slicing settings, ensuring optimal results for their specific design and printing requirements.
The practical applications of understanding the connection between slicing engines and product design software for 3D printing are far-reaching. It allows designers and engineers to optimize print quality, reduce printing time, minimize material waste, and troubleshoot printing issues effectively. By leveraging the capabilities of slicing engines, they can produce high-quality 3D printed parts that meet the desired functional and aesthetic requirements, driving innovation and advancing various industries.
Support generation
Support generation is a crucial aspect of product design software for 3D printing, ensuring the successful production of complex geometries and intricate designs. It involves creating temporary structures that provide support to overhanging features and prevent deformation during the printing process.
-
Automatic support generation
This feature analyzes the 3D model and automatically generates support structures, eliminating the need for manual placement and saving time. -
Manual support placement
For greater control and customization, users can manually position support structures in specific areas of the model, ensuring optimal support for complex geometries. -
Support density control
Design software allows users to adjust the density and thickness of support structures, balancing support strength and material usage. -
Breakaway support materials
Some software supports the use of breakaway materials for support structures, which can be easily removed post-printing without damaging the main model.
Support generation plays a critical role in 3D printing, enabling the production of parts with complex geometries that would be difficult or impossible to manufacture using traditional methods. It streamlines the design process, reduces the risk of print failures, and enhances the overall quality of 3D printed parts.
Build optimization
Build optimization is a critical aspect of product design software for 3D printing, enabling designers to maximize the efficiency and effectiveness of the printing process. It involves optimizing various parameters, such as print orientation, layer thickness, and infill patterns, to achieve the desired part quality, strength, and material usage.
Product design software with built-in build optimization tools provides users with automated or manual control over these parameters, allowing them to fine-tune the printing process for specific materials and models. Real-life examples include slicing software like Cura and Simplify3D, which offer advanced build optimization features, including layer-by-layer customization, support structure generation, and print path optimization.
The practical applications of understanding the connection between build optimization and product design software for 3D printing are far-reaching. It enables designers to reduce printing time, minimize material waste, improve part strength, and enhance surface quality. By optimizing the build process, designers can produce high-quality 3D printed parts that meet the desired functional and aesthetic requirements, driving innovation and advancing various industries.
Integration with CAD
Integration with computer-aided design (CAD) software is a critical aspect of product design software for 3D printing, enabling a seamless workflow from design conception to physical realization.
CAD software provides precise 3D modeling capabilities, allowing designers to create detailed and accurate digital representations of their designs. By integrating CAD software with product design software for 3D printing, designers can directly import their CAD models into the latter, eliminating the need for manual conversion and reducing the risk of errors.
Real-life examples of CAD integration within product design software for 3D printing include Siemens NX, Dassault Systmes SolidWorks, and Autodesk Fusion 360. These software packages offer seamless integration between CAD and 3D printing capabilities, enabling designers to optimize their designs for additive manufacturing and generate print-ready files efficiently.
The practical applications of understanding the connection between integration with CAD and product design software for 3D printing are numerous. It streamlines the design workflow, reduces design errors, and enables designers to leverage the full potential of both CAD and 3D printing technologies. By integrating CAD software with product design software for 3D printing, designers can accelerate product development, reduce costs, and bring innovative products to market faster.
Cloud collaboration
Cloud collaboration is rapidly transforming product design software for 3D printing, enabling designers and engineers to seamlessly collaborate on projects, share designs, and access computing resources from anywhere with an internet connection.
-
Real-time collaboration
Multiple users can simultaneously access and edit the same design, facilitating efficient teamwork and reducing design cycles. -
Centralized data management
Cloud-based platforms provide a central repository for design files, ensuring that everyone has access to the latest version and eliminating the risk of data loss. -
Remote access
Designers and engineers can access their projects from any location with an internet connection, enabling flexible working arrangements and global collaboration. -
Scalable computing resources
Cloud platforms offer on-demand access to powerful computing resources, enabling complex simulations and large-scale 3D modeling without the need for expensive local infrastructure.
Cloud collaboration empowers product design teams to work more efficiently, reduce design errors, and accelerate product development. It breaks down geographical barriers, fosters innovation, and empowers teams to bring groundbreaking products to market faster.
User interface
User interface (UI) plays a critical role in product design software for 3D printing, as it directly influences the user experience and productivity of designers and engineers. An intuitive and well-designed UI enables users to interact with the software efficiently, access essential tools and features effortlessly, and navigate complex workflows seamlessly.
A well-designed UI in product design software for 3D printing streamlines the modeling process, reduces design errors, and shortens learning curves for novice users. It empowers designers to focus on their creativity and innovation, rather than struggling with cumbersome or unintuitive software. Real-life examples of user-friendly UI in product design software include Dassault Systmes SolidWorks, Siemens NX, and Autodesk Fusion 360, which offer customizable toolbars, context-sensitive menus, and visual feedback to enhance user experience.
Understanding the connection between UI and product design software for 3D printing is crucial for software developers and UX designers. By prioritizing user-centered design principles, they can create software that empowers users to design and create innovative products more efficiently and effectively. This understanding also enables users to make informed decisions when selecting product design software, ensuring that they have the tools they need to succeed in their design endeavors.
File formats
File formats play a crucial role in product design software for 3D printing, serving as the foundation for storing, sharing, and interpreting 3D models. The choice of file format affects the compatibility, accessibility, and quality of the design data throughout the workflow.
One of the key aspects of file formats is their ability to capture and represent the intricacies of 3D models. Formats like STL (STereoLithography) and AMF (Additive Manufacturing File) are widely used in product design software for 3D printing due to their ability to represent complex geometries and support various 3D printing technologies. These formats provide a common ground for exchanging and sharing 3D models between different software applications and 3D printers.
Furthermore, file formats also influence the efficiency and effectiveness of the 3D printing process. Formats that support lossless compression, such as PLY (Polygon File Format) and 3MF (3D Manufacturing Format), allow for the preservation of fine details and accurate representation of the original 3D model. This is particularly important for applications where precision and surface quality are critical, such as in medical and dental 3D printing.
Understanding the connection between file formats and product design software for 3D printing empowers designers and engineers to make informed decisions when selecting the appropriate format for their specific needs. By considering factors such as compatibility, accuracy, and efficiency, they can ensure that their designs are effectively communicated and accurately realized through the 3D printing process.
FAQs on Product Design Software for 3D Printing
This section addresses frequently asked questions about product design software for 3D printing, clarifying key concepts and providing practical guidance.
Question 1: What are the key features of product design software for 3D printing?
Product design software for 3D printing offers capabilities such as 3D modeling, simulation, material selection, slicing, support generation, build optimization, integration with CAD, cloud collaboration, and user-friendly interfaces.
Question 2: How does product design software for 3D printing differ from traditional CAD software?
While traditional CAD software focuses on designing 2D and 3D models for manufacturing, product design software for 3D printing is specifically tailored for preparing models for additive manufacturing, considering factors like layer-by-layer deposition and material properties.
Question 3: What are the benefits of using product design software for 3D printing?
Product design software for 3D printing streamlines the design process, enables design optimization, reduces errors, facilitates collaboration, and supports the creation of complex geometries that may be difficult to manufacture using traditional methods.
Question 4: What are some popular examples of product design software for 3D printing?
Leading examples of product design software for 3D printing include Siemens NX, Dassault Systmes SolidWorks, Autodesk Fusion 360, and PTC Creo.
Question 5: What factors should be considered when choosing product design software for 3D printing?
When selecting product design software for 3D printing, consider factors such as modeling capabilities, simulation tools, material libraries, slicing engines, cloud collaboration features, user interface, and compatibility with your existing workflow.
Question 6: How can I learn more about product design software for 3D printing?
Numerous resources are available online, including tutorials, documentation, and user communities. Additionally, attending workshops or training sessions can provide hands-on experience and in-depth knowledge.
These FAQs provide a glimpse into the capabilities and applications of product design software for 3D printing. As this technology continues to advance, it is transforming product design and manufacturing processes, opening up new possibilities for innovation and customization.
In the next section, we will delve deeper into the technical aspects of product design software for 3D printing, discussing advanced modeling techniques, simulation methods, and emerging trends.
Tips for Utilizing Product Design Software for 3D Printing
This section provides practical tips for effectively using product design software for 3D printing, helping you optimize your workflow and achieve successful results.
Tip 1: Understand the capabilities and limitations of your software. Familiarize yourself with the modeling tools, simulation capabilities, and other features offered by your software. This will help you determine its suitability for your specific design needs.
Tip 2: Choose the right material for your design. The choice of material can significantly impact the strength, durability, and functionality of your printed part. Carefully consider the material properties and printing parameters to ensure optimal performance.
Tip 3: Optimize your model for 3D printing. Prepare your model for printing by checking for errors, ensuring proper orientation, and adding supports as necessary. This will help minimize printing errors and improve part quality.
Tip 4: Use simulation tools to validate your design. Simulation capabilities can help you analyze the structural integrity, fluid dynamics, and other aspects of your design before printing. This allows you to identify potential issues and make necessary adjustments.
Tip 5: Collaborate with others using cloud-based platforms. Cloud collaboration features enable you to share designs, work on projects with team members, and access computing resources from anywhere. This streamlines the design process and fosters innovation.
Tip 6: Stay updated with the latest software versions and industry trends. Regular software updates often include new features and improvements. Keeping up with industry trends will help you leverage emerging technologies and best practices.
Tip 7: Practice and experiment with different design techniques. Hands-on experience is crucial for mastering product design software for 3D printing. Experiment with different modeling techniques, materials, and printing parameters to expand your skills and knowledge.
Tip 8: Seek support from online communities and forums. Engage with experienced users and experts in online communities and forums. These platforms offer valuable resources, technical advice, and troubleshooting assistance.
By following these tips, you can effectively utilize product design software for 3D printing, enhance your design capabilities, and produce high-quality printed parts. This will enable you to fully harness the potential of 3D printing technology and bring your innovative ideas to life.
The insights gained from these tips will serve as a solid foundation for the concluding section of our article, where we will discuss the future prospects and transformative impact of product design software for 3D printing on various industries and applications.
Conclusion
Our exploration of product design software for 3D printing has revealed its transformative impact on product development and manufacturing. This software empowers designers and engineers to create complex geometries, optimize designs for additive manufacturing, and produce high-quality 3D printed parts.
Key insights from this article include:
- Product design software for 3D printing integrates modeling, simulation, and slicing capabilities, enabling efficient and precise design for additive manufacturing.
- The use of advanced materials and simulation tools enhances the structural integrity, functionality, and aesthetics of 3D printed parts.
- Cloud collaboration and user-friendly interfaces empower teams to work seamlessly, share designs, and access computing resources from anywhere.
As we look ahead, product design software for 3D printing will continue to evolve, unlocking even greater possibilities. It will enable the creation of personalized products, drive innovation in industries such as healthcare and aerospace, and contribute to a more sustainable manufacturing landscape. The future of product design lies in the seamless integration of digital tools and additive manufacturing technologies, empowering designers and engineers to bring their most innovative ideas to life.
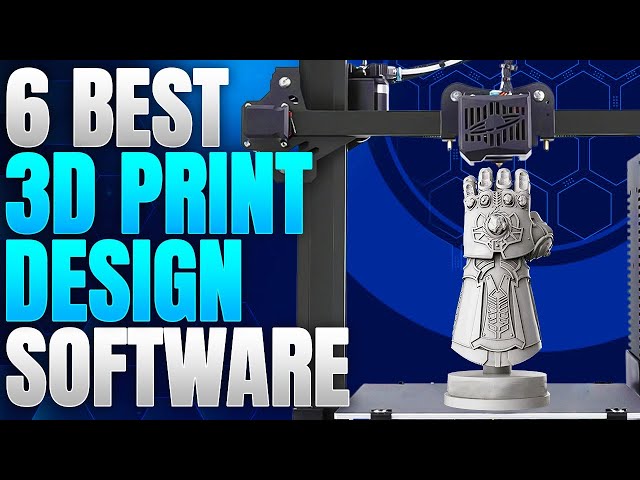